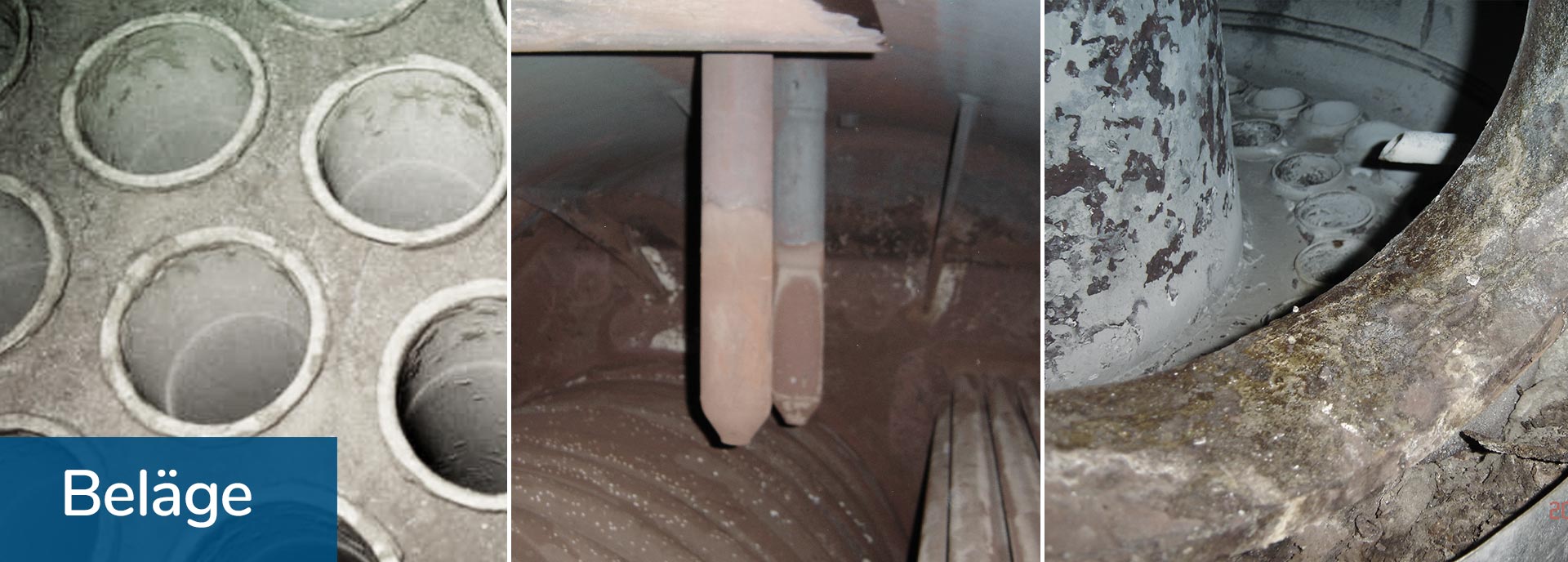
Entstehung und Vermeidung von Belägen
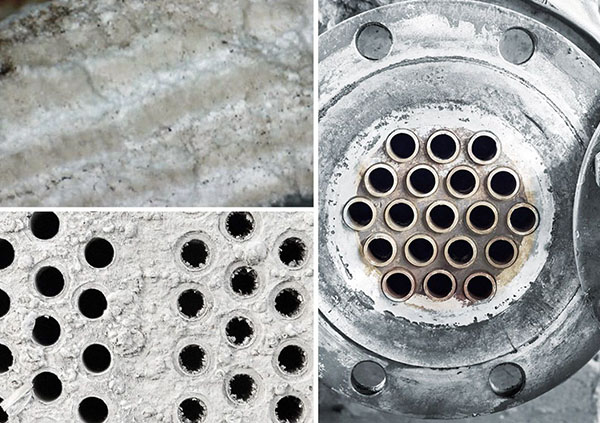
Die Entstehung von Belägen kann durch verschiedene Faktoren begünstigt werden, wie z.B. chemische Reaktionen, Temperatur, Druck und Löslichkeiten der beteiligten Substanzen, wie beispielsweise Wasser, produziertes Lebensmittel etc.
Es gibt verschiedene Arten von Belägen, die je nach Industrie und den spezifischen Bedingungen variieren können. Einige der häufigsten Arten sind:
Kalkablagerungen: Sie entstehen durch die Kristallisation von Calcium- und Magnesiumsalzen aus hartem Wasser. Kalkablagerungen können in Rohrleitungen, Wärmetauschern und anderen Ausrüstungen auftreten und die Durchflussraten reduzieren sowie die Effizienz beeinträchtigen.
- Rost und Korrosionsbeläge: Diese Art von Belägen tritt auf Metalloberflächen auf, wenn diese mit Feuchtigkeit und Sauerstoff in Kontakt kommen. Rost kann die Integrität von Metallstrukturen beeinträchtigen und zu schwerwiegenden Schäden führen.
- Organische Ablagerungen: Sie können aus organischen Verbindungen wie Ölen, Fetten, Proteinen oder anderen biologischen Materialien bestehen.
- Biofilme: Dabei handelt es sich um sind komplexe Gemeinschaften von Mikroorganismen, die sich auf Oberflächen ansiedeln und dort eine Schutzschicht bilden. Diese können hartnäckig sein und schwer zu entfernen sein.
Um Beläge in der Industrie zu vermeiden oder zu reduzieren, können verschiedene Maßnahmen ergriffen werden:
- Regelmäßige Reinigung und Instandhaltung: Eine regelmäßige Reinigung der Ausrüstung und Oberflächen kann dazu beitragen, die Bildung von Belägen zu minimieren.
- Verwendung von Additiven: In einigen Fällen können spezielle Additive in den Produktionsprozess eingeführt werden, um die Bildung von Belägen zu verhindern oder zu reduzieren.
- Kontrolle von Prozessparametern: Die Kontrolle von Prozessparametern wie Temperatur, Druck und pH-Wert kann dazu beitragen, die Bildung von Belägen zu reduzieren.
- Entkalkung und Entrostung: In manchen Fällen ist es notwendig, regelmäßige Entkalkungs- und Entrostungsverfahren durchzuführen, um bereits entstandene Beläge zu entfernen.
- Einsatz von Filtrations- und Separationstechniken: Durch den Einsatz von Filtrations- und Separationstechniken können Verunreinigungen aus Flüssigkeiten und Gasen entfernt werden, wodurch die Bildung von Belägen minimiert wird.
In den nachfolgenden Darstellungen fokussieren wir uns vorwiegend auf die verschiedenen Arten von Kalkablagerungen in den Zuckerfabriken. Wir geben einen Überblick über Ablagerungen, wobei der Schwerpunkt auf Rübenzucker / Rübenzuckerfabriken liegt, zeigen aber auch Aspekte auf, die spezifisch für die Rohrzuckerproduktion sind. Bei den Ablagerungen in der Zuckerindustrie sind es vornehmlich Kalkablagerungen, die auftreten.
Kesselsteinbildung
Bei Kalkablagerungen spricht man auch häufig von „Kesselstein“, auch als Kesselsteinablagerungen bezeichnet.
Es ist ein typischer Belag, der in Dampfkesseln und Heizungsanlagen auftritt. Es handelt sich um eine feste Ablagerung aus Kalk, die sich bildet, wenn hartes Wasser, mit einem hohen Gehalt an Calcium- und Magnesiumsalzen, erhitzt wird.
Wenn Wasser erhitzt wird, können sich die in ihm enthaltenen, gelösten Mineralien auskristallisieren und als Kesselstein auf den Innenflächen der Kessel, Rohrleitungen und Wärmetauschern ablagern. Die Kesselsteinbildung kann die Effizienz der Heizungsanlagen und Dampfkessel beeinträchtigen, da die Ablagerungen die Wärmeübertragung behindern und die Energiekosten erhöhen. Außerdem können Kesselsteinablagerungen Korrosion fördern und damit die Lebensdauer der Anlagen verkürzen.
Die Zusammensetzung des Kesselsteines wird mit Hilfe einer Kombination spezifischer modifizierter Methoden analysiert, darunter:
- ICP-OES (induktiv gekoppeltes Plasma – optische Emissionsspektrometrie)
- Ionenchromatographie-
- Titrationsmethoden
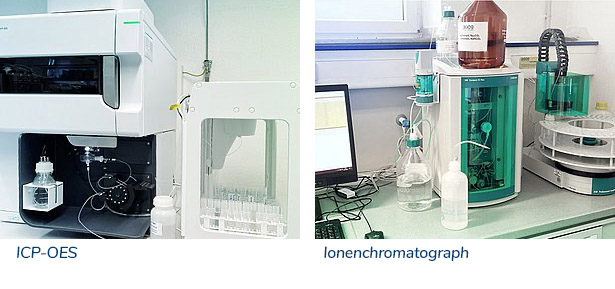
KEBO hat bisher über 10.000 Kesselstein-Proben analysiert, die über einen Zeitraum von mehr als 40 Jahren in über 1.000 Fabriken in rund 60 Ländern gesammelt wurden.
Neben einigen Prozessänderungen, die die Bildung einer bestimmten Art von Kesselstein reduzieren, gibt es zwei Haupttechniken zur Kesselsteinvermeidung:
- die Verwendung von Ionenaustauschern zum Ersatz von Kalzium durch Natrium- oder Wasserstoffkationen und
- die Verwendung von Antiscalants zur Stabilisierung der kesselsteinbildenden Verbindungen in einem mikrokristallinen Zustand
In den nachfolgenden Darstellungen zeigen wir die wesentlichen Kalkablagerungen auf, die es in der Zuckerindustrie gibt.
Die wichtigsten Kesselstein-Bestandteile
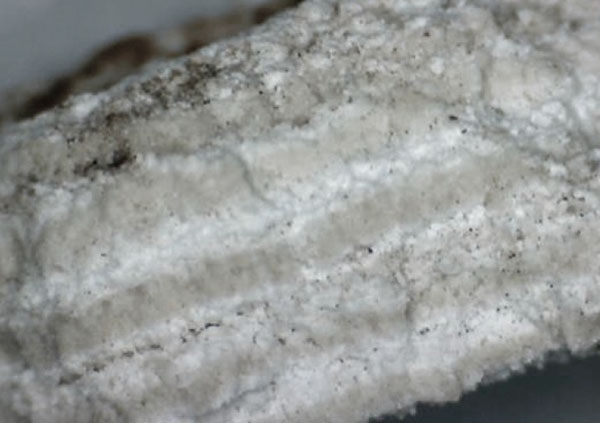
Die wichtigsten Kesselstein-Bestandteile sind Kalziumsalze, Silikate und manchmal Zuckerkohle. Weitere anorganische Zunderbestandteile sind von untergeordneter Bedeutung oder eher Sonderfälle. Neben der chemischen Zusammensetzung wird die Entfernung von Kesselstein durch seine Struktur beeinflusst. Ein aus Schichten aufgebauter Zunder (siehe Abb.) ist oft schwieriger zu entfernen und kann eine wiederholte chemische Behandlung erfordern.
Calciumoxalat
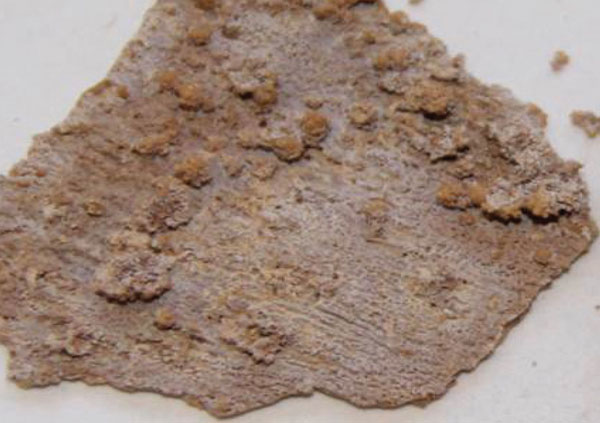
Calciumoxalat kommt in Rüben- und Rohrzuckerfabriken vor und entsteht in den Kulturen durch verschiedene Reaktionen aus Vorläufersubstanzen. Es ist nach wie vor der wichtigste Kesselstein-Bestandteil in der Zuckerindustrie und schränkt die Betriebszeit ein, wenn der Saft nicht behandelt wird. Calciumoxalat-haltige Beläge weisen eine große Variation an Farben und Strukturen auf. Beispiele sind in den Abbildungen 2 und 3 dargestellt.
Calciumoxalat ist in alkalischen oder sauren Reinigungslösungen nicht löslich, daher ist eine Reinigung in zwei Schritten erforderlich. Im ersten, alkalischen Schritt wird das Oxalat durch Natriumcarbonat, das der alkalischen Reinigungslösung im Überschuss zugesetzt wird, in Calcium-Carbonat umgewandelt.
Der Reinigungslösung werden Dispergier- und Netzmittel hinzugefügt, um ihr Eindringen in den Zunder zu verbessern und eine vollständige Umwandlungsreaktion nicht nur an der Oberfläche des Zunders zu erreichen.
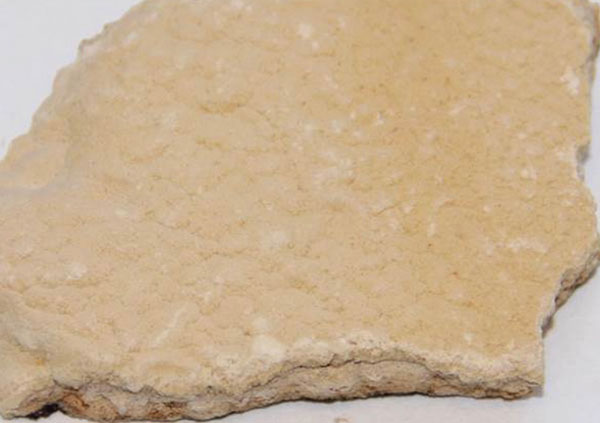
Im zweiten, sauren Schritt wird das gebildete Calciumcarbonat mit einer Säure gelöst, die zum Schutz der Anlage einen Korrosionsinhibitor enthält.
In der Praxis werden Ameisen-, Sulfam- oder Chlorwasserstoffsäure verwendet. Die Bildung von Calciumoxalat-Ablagerungen wird in der europäischen Zuckerindustrie nicht mehr als Problem angesehen, da ihre Bildung durch die Enthärtung von Dünnsaft, den Einsatz von Antiscalant auf Polyacrylat-Basis oder eine Kombination beider Techniken gut verhindert werden kann.
Calciumcarbonat
Calciumcarbonat entsteht in Zuckerfabriken bei der „Carbonatisierung“ in Wärmetauschern für gekalkten/karbonisierten Saft als Folge der Zugabe von Kalkmilch oder Saccharat und CO2. Manchmal findet man Calciumcarbonat auch in Verdampfer-Stationen, was auf einen Optimierungsbedarf im Carbonatisierungs-Prozess hinweist, wie z.B. die Verbesserung der Reaktionszeiten oder die Verbesserung der Filtration.
Durch reduzierten Kalkeinsatz und weitere Optimierung der Saftreinigung in der europäischen Zuckerindustrie nimmt allerdings die Bedeutung von Calciumcarbonat als Kesselsteinkomponente ab.
Beläge, deren Zusammensetzung überwiegend aus Calciumcarbonat besteht, können durch Lösen mit inhibierter Säure entfernt werden. Die Bildung und Ausfällung von Calciumcarbonat ist die erwünschte Reaktion während der Carbonatisierung. In den Verdampfer-Stationen oder in weiteren Prozessschritten kann die Bildung durch Optimierung der Carbonatisierung verhindert werden, z.B. durch Enthärtung des Dünnsaftes oder die Anwendung von Antiscalant auf Polyacrylat-Basis.
Calciumsulfat und Calciumsulfit
Calciumsulfat oder Calciumsulfit findet sich gelegentlich in den Belägen von Zuckerfabriken mit „Sulfatierung“. Es entsteht durch den Zusatz von zu viel SO2 oder (Bi-)Sulfit. In einigen Gebieten führt ein hoher Sulfatgehalt im Zuckerrohr auch ohne Sulfatierung zu Calciumsulfat-Belägen. Für die Rohrzuckerindustrie ist diese Art von Kesselstein von zunehmender Bedeutung, da der Trend zur Herstellung von farbarmen Rohzucker und Plantagenweißzucker geht.
Für die Entfernung von Calciumsulfit bzw. -sulfat-Belägen wird eine Umwandlung mit Natrium-Carbonat – wie oben für Oxalat beschrieben – empfohlen, da Sulfit bei direkter Behandlung mit Säure gasförmiges SO2 bildet.
Calciumphosphat
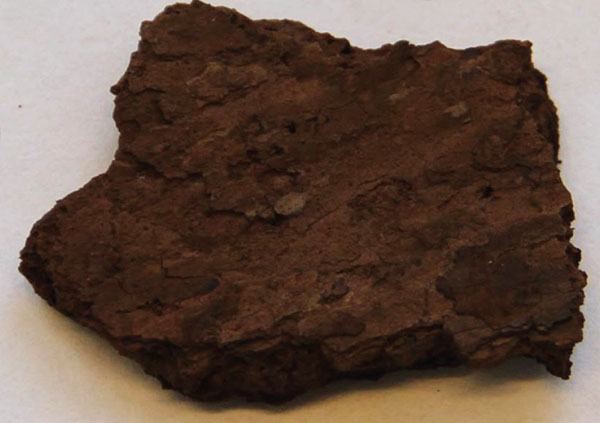
Calciumphosphat ist die wichtigste Verbindung, die in Rohrzuckerfabriken in der Anfangsphase auftritt und deren Betriebszeit einschränkt. Es kann durch saure Reinigung mit inhibierter Ameisen- oder Salzsäure entfernt werden. Das meiste Calciumphosphat gelangt als Partikel und nicht als gelöste Ionen in die Verdampfer. Calciumphosphathaltige Beläge weisen oft eine weniger dichte, aber dicke Struktur (Abb. 5) und eine dunkle Farbe auf, was darauf hindeutet, dass sie aus Schlammpartikeln und nicht aus der Kristallisation von Ionen entstanden sind. Die wirksamste Vorbeugung ist daher die Optimierung des Saftreinigungsprozesses, insbesondere bei der Sedimentation und Filtration. Calciumphosphat-Ablagerungen, die später durch Kristallisation entstehen, können durch die Verwendung von Antiscalant auf Polyacrylat-Basis verhindert werden.
Calciumaconitat
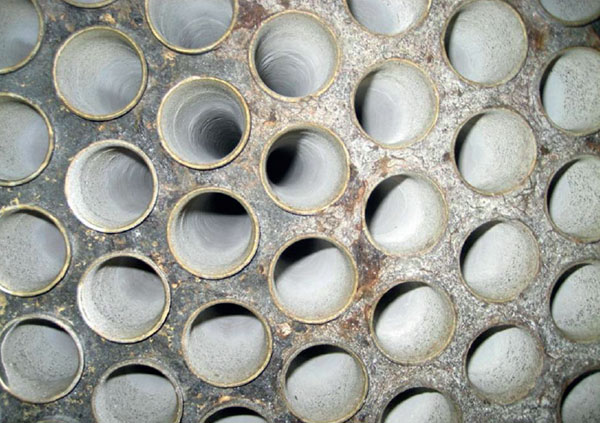
Calciumaconitat ist eine der wesentlichen Belagarten in Südamerika. Wenn der Saft nicht behandelt wird, kann es zu bedeutenden Betriebsstörungen mit Spätfolgen führen.
Insbesondere mechanisch sind Calciumaconitatbeläge sehr schwierig zu entfernen. Chemisch – mit Ameisensäure und einem Inhibitor – lassen sie sich leicht entfernen. Die Bildung von Calciumaconitat kann durch die Anwendung von Antiscalantien auf Polyacrylat-Basis verhindert werden.
Calciumcitrat
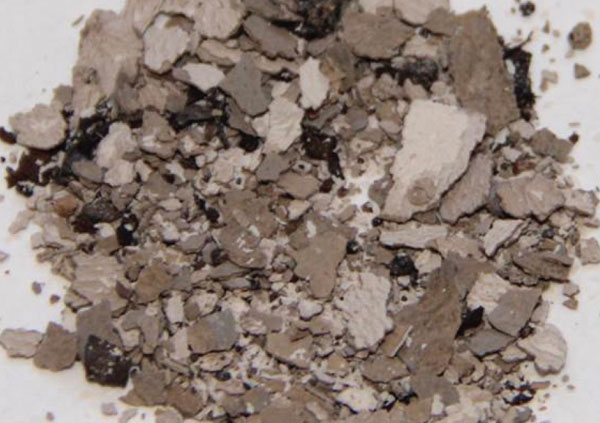
Wenn Zitronensäure zur chemischen Reinigung von Verdampfern verwendet wird, kann sich ein Calcium-Citrat-Kesselstein bilden, da der lösliche Calcium-Citrat-Komplex, der von Reinigungsanwendungen bei niedrigen Temperaturen bekannt ist, bei hohen Temperaturen nicht stabil ist. Daher wird Zitronensäure nicht für die Reinigung von Verdampfern bei hohen Temperaturen empfohlen.
Silikate
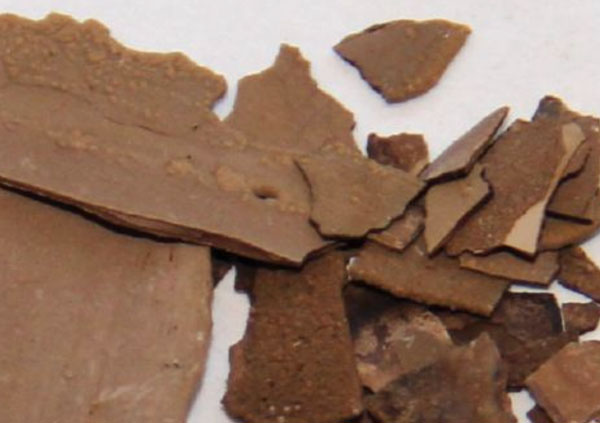
Silikate kommen in Rüben- und Rohrzuckerfabriken vor. Während in der Rohrzuckerindustrie Silikate aus dem Zuckerrohr stammen, ist die Hauptquelle für Silikate in der Rübenzuckerindustrie der Kalkstein. Im Zunder ist Silikat meist nicht als einfaches Silikat vorhanden. Silikate im Zunder haben komplexe polymere Strukturen und treten besonders in Rübenzuckerfabriken oft als Aluminium-, Magnesium- und Calciumsilikate auf.
- Vorbeugung: Der Silikatgehalt steigt mit sinkendem pH-Wert an der Einsatzstelle, daher: keine frische Kalkmilch zur zweiten Karbonatisierung.
- Prävention für Rohrzuckerfabriken: Anwendung von Antiscalant auf Polyacrylatbasis
Zuckerkohle und karamellisierter Zucker
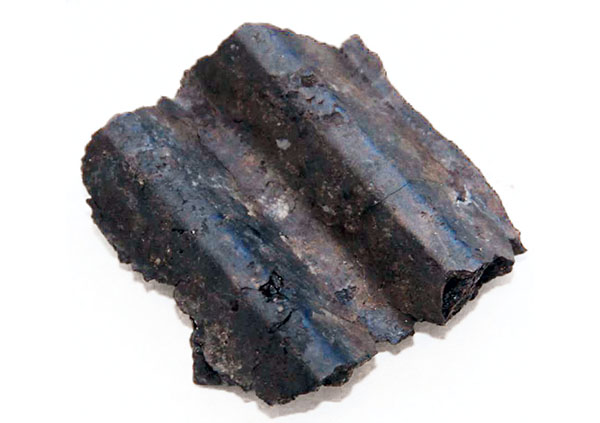
Zuckerkohle und karamellisierter Zucker entstehen, wenn Zucker auf heißen Oberflächen verbrannt wird. Dies geschieht häufig als Unfall bei einer Stromunterbrechung oder einer anderen unerwarteten Störung. Diese Art der Verkrustung zeigt eine zunehmende Tendenz, vor allem weil das Unfallrisiko mit zunehmender Dauer der Kampagne steigt. Aus einer wachsenden Zahl von Fabriken werden Ausfälle gemeldet, die durch interne und externe Probleme mit den Stromnetzen verursacht werden. Darüber hinaus hat der Erfolg von Fallfilm- und Plattenverdampfern in der Zuckerindustrie das Risiko für solche Zunder erhöht, da diese Verdampfer-Typen im Falle eines Ausfalls empfindlicher für die Bildung von Zuckerkohle sind (Abb.).
Wenn die Rohre oder der Raum zwischen den Platten nicht vollständig verstopft sind, kann die Zuckerkohle mit einer alkalischen Lösung entfernt werden, die Suspensionsmittel und Netzmittel enthält. Das Suspensionsmittel ist wichtig, weil der Kesselstein durch die Lösung oft von der Oberfläche entfernt, aber nicht zu 100 % gelöst wird. Moderne Verdampfer verfügen über ein Notfallsystem für die Wasserversorgung im Falle einer Störung, um die Bildung von Zuckerkohle zu vermeiden. In Fällen, in denen Zucker während des Standardbetriebs karamellisiert, kann eine Optimierung der Saftverteilung des Saftverteilungssystems das Problem verringern.
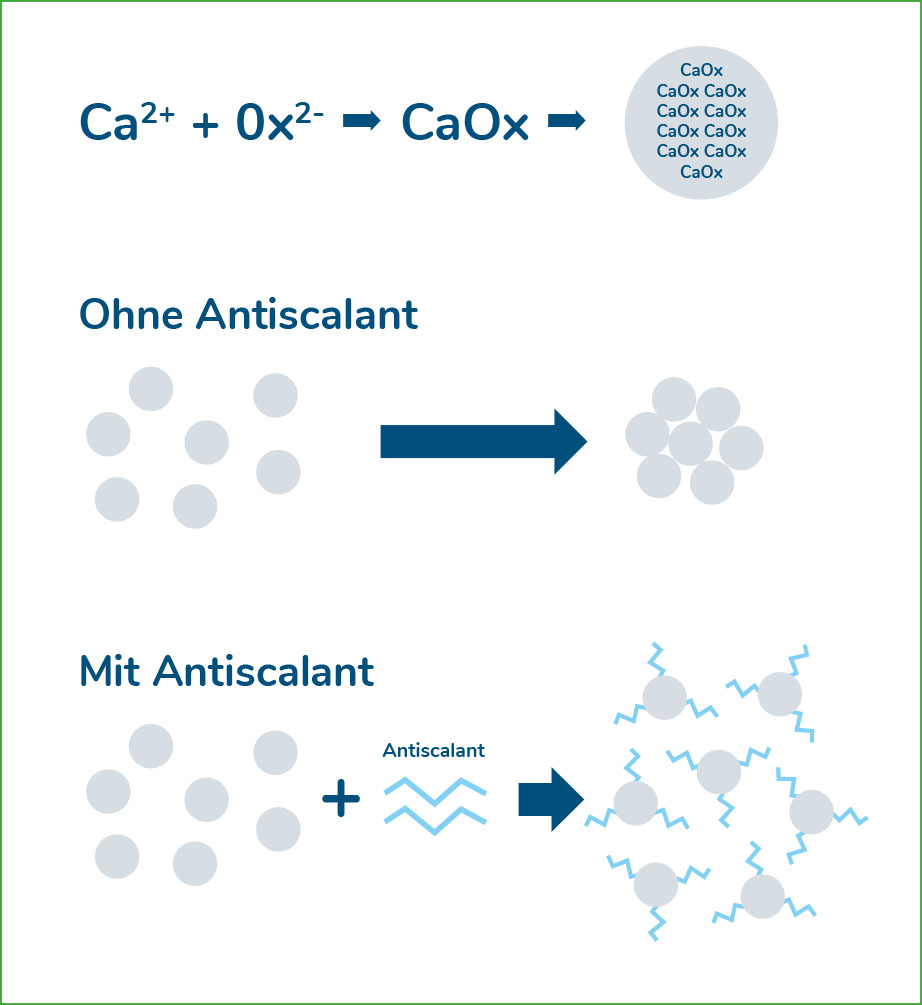
Antiscalants
Antiscalants für die Verwendung in Zuckersaft basieren auf Polyacrylat und diese Chemikalie ist durch nationale und internationale Vorschriften beschränkt. Ein Antiscalant auf Polyacrylat-Basis verhindert die Bildung von Kesselstein, indem es kleine, noch unsichtbare Mikrokristalle aus Kalziumsalzen stabilisiert, die sich bei der Verdampfung und Konzentration des Saftes bilden. Ohne Antiscalant wachsen die Mikrokristalle, kleben zusammen und bilden auf diese Weise Kesselstein. Das Antiscalant ist in der Lage, sich mit einem Ende seiner Molekülkette an die Oberfläche der Mikrokristalle zu heften und sie am weiteren Wachstum zu hindern. Dadurch bleiben die Mikrokristalle im Saft stabil, so dass sie sich aus technischer Sicht so verhalten, als wären sie noch in Lösung.
Die auf unserer Webseite dargestellten Produkte sind nur eine Auswahl unseres gesamten Programms. Die Vielzahl der denkbaren Reinigungsprobleme erfordert eine eingehende Beratung, um die maßgeschneiderte Lösung mit dem passenden Produkt zu finden. Gleiches gilt auch für den Korrosionsschutz, bei der Wasserkonditionierung und -aufbereitung, der Belagverhinderung und bei der Schaumbildung in industriellen Anwendungen.
Sprechen Sie mit uns, wir helfen Ihnen gerne weiter!
Auf Wunsch können wir in unserem Labor Beläge analysieren und auf Basis unserer langjährigen Erfahrung eine Reinigungsstrategie unter Berücksichtigung der Gegebenheiten vor Ort entwickeln.